Mastering the Art of Welding: Just How to Avoid Undercut Welding Issues for Flawless Manufacture Results
Effectiveness and precision are vital on the planet of welding, where also the slightest flaw can endanger the structural honesty of a fabricated piece. One usual challenge that welders face is undercutting, an issue that can lead and damage a weld joint to costly rework. By comprehending the source of undercut welding and executing efficient strategies to avoid it, welders can boost their craft to new degrees of excellence (Preventing weld undercut). In the quest of perfect manufacture results, understanding the art of welding to avoid undercut concerns is not just a skill but a necessity for those striving for perfection in their work.
Recognizing Undercut Welding

To avoid undercut welding, welders need to ensure correct welding specifications, such as adjusting the present, voltage, travel rate, and preserving the appropriate electrode angle. Furthermore, using the proper welding technique for the particular joint arrangement is essential. Employing weaving movements or backstepping techniques can help make sure correct weld metal deposition and minimize the chance of undercut formation. Routine assessment of welds throughout and after the welding procedure is also crucial to capture any undercut very early and make needed modifications to avoid more issues. Preventing weld undercut. By recognizing the reasons of undercut welding and executing safety nets, welders can accomplish high-grade, structurally sound welds.
Root Causes Of Undercut in Welding
Comprehending the factors that contribute to damage in welding is vital for welders to produce top notch, structurally sound welds. Insufficient welding incorrect or present welding rate can also contribute to damage. Recognizing these causes and executing appropriate welding strategies can help avoid damaging concerns, ensuring strong and long lasting welds.
Techniques to stop Undercutting

To minimize the threat of damaging in welding, welders can employ tactical welding techniques aimed at boosting the top quality and stability of the weld joints. Furthermore, utilizing the pop over to this web-site correct welding technique for the details joint arrangement, such as weave or stringer grains, can contribute to reducing damaging.
In addition, appropriate joint preparation, including ensuring clean base products without pollutants and using the appropriate welding consumables, is crucial in protecting against undercut problems. Utilizing back-step welding techniques and regulating the weld bead account can likewise help disperse warm evenly and lessen the danger of undercut. Normal assessment of the weld joint during and after informative post welding, along with executing quality guarantee steps, can assist in finding and addressing damaging problems without delay. By carrying out these strategies vigilantly, welders can attain perfect manufacture results with minimal undercut flaws.
Importance of Appropriate Welding Specifications
Picking and maintaining suitable welding specifications is necessary for achieving successful welds with minimal problems. Welding specifications describe variables such as voltage, existing, take a trip rate, electrode angle, and shielding gas flow rate that directly affect the welding procedure. These specifications have to be carefully adjusted based on the type of material being welded, its thickness, and the welding technique employed.
Proper welding parameters guarantee the best amount of warm is related to thaw the base metals and filler material uniformly. If the parameters are set as well high, it can result in too much warm input, causing spatter, distortion, or burn-through. On the various other hand, if the specifications are as well reduced, insufficient combination, lack of infiltration, or undercutting may occur.
Quality Control in Welding Procedures
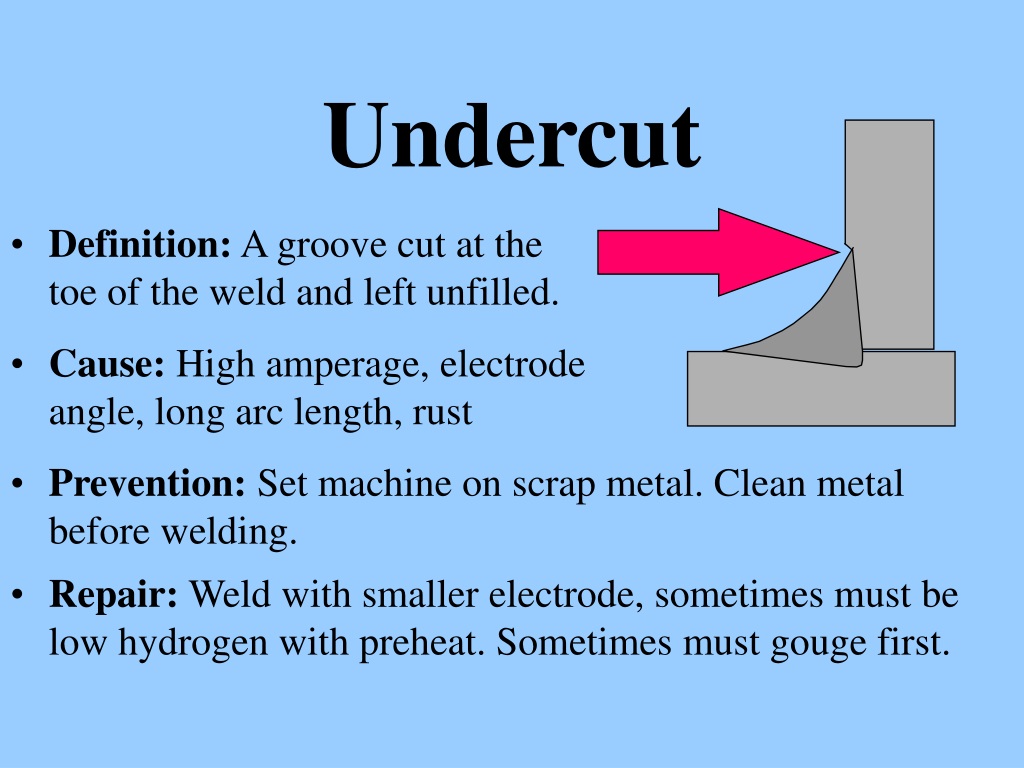
Final Thought
Finally, mastering the art of welding calls for a complete understanding of undercut welding, its causes, and strategies to stop it. By ensuring correct welding specifications and implementing top quality assurance techniques, perfect fabrication outcomes can be achieved. useful link It is crucial for welders to constantly strive for quality in their welding operations to prevent undercut issues and create top quality welds.
Undercut welding, an usual problem in welding procedures, occurs when the weld steel doesn't appropriately fill the groove and leaves a groove or anxiety along the bonded joint.To avoid undercut welding, welders need to guarantee correct welding specifications, such as adjusting the present, voltage, traveling speed, and preserving the proper electrode angle. Inadequate welding existing or incorrect welding rate can also contribute to damage.To mitigate the risk of damaging in welding, welders can use strategic welding methods intended at boosting the top quality and integrity of the weld joints.In final thought, understanding the art of welding calls for an extensive understanding of undercut welding, its reasons, and strategies to stop it.